MITRE collaborated with industry partners to demonstrate how additive manufacturing (3D printing) could improve undersea acoustic sensing. Our compact and low-power transducer prototype offers a unique capability for ocean missions requiring high sensitivity—and sometimes laser-sharp focus.
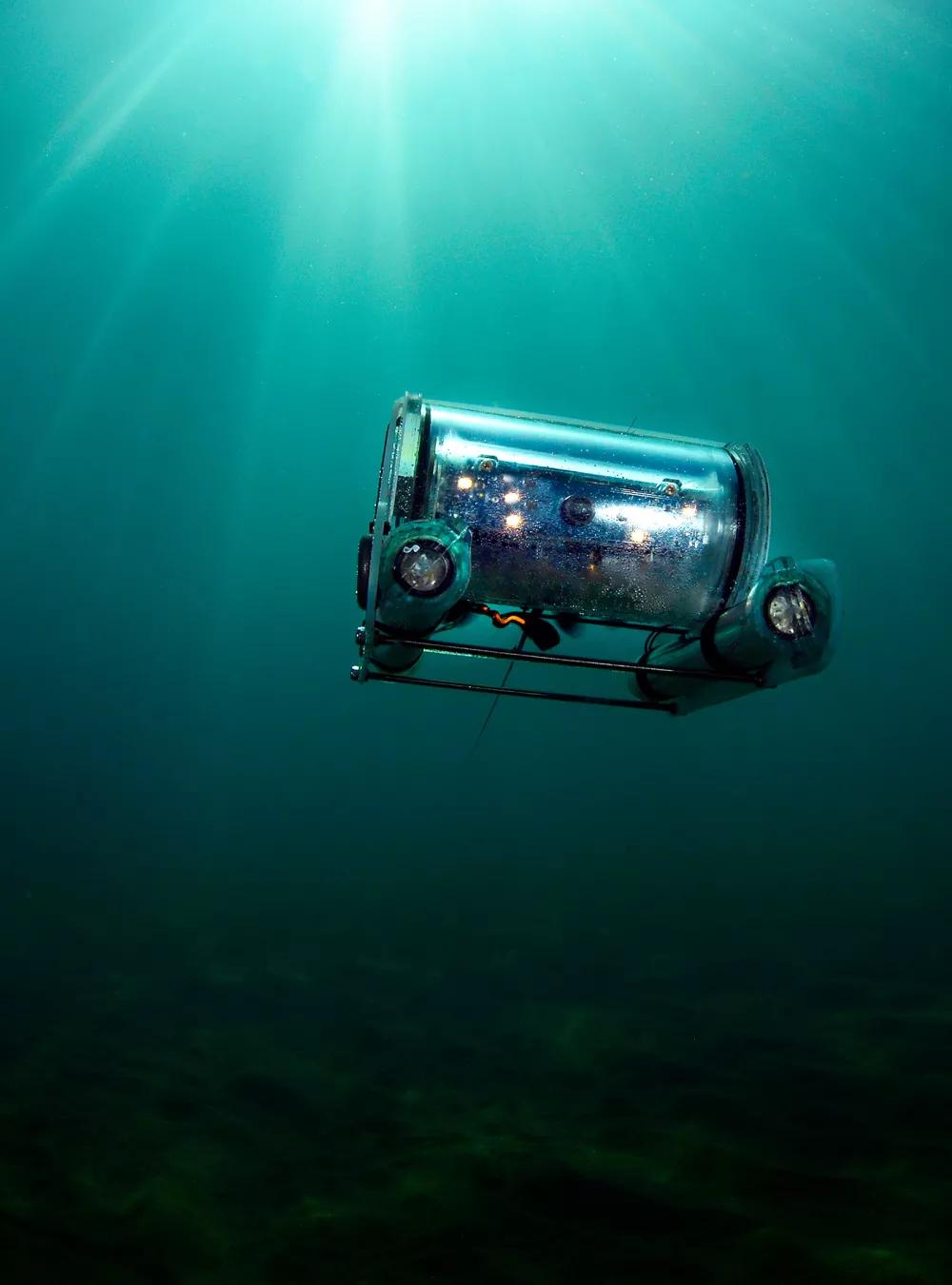
Beneath the Deep: 3D Printing Opens Novel Wave of Maritime Opportunities
If the demise of the Titan submersible in June showed us anything, it’s that the ocean can be an unforgiving, bewildering space. From celebrity researcher Jacques Cousteau to Titanic-discoverer Robert Ballard, undersea explorers have long sought to know the unknowable.
Cousteau called the oceans “...the great unifier...man’s only hope”—perhaps foreseeing the key role oceans play in national security, economic stability, and climate resilience.
But big opportunities often come with big challenges. For example, below the surface of that “great unifier,” acoustics can wreak havoc on maritime activities. That’s why MITRE’s BlueTech team led a collaborative initiative to improve our ability to communicate below the surface.
Inspired by the R&D 100-winning FUSE antenna, another MITRE-developed capability, we set out to determine how to “print” transducers, the sensors that send and receive acoustic signals underwater.
Through our independent R&D program, we connected with two industry partners that bring key expertise in 3D printing, also called additive manufacturing. MSI Transducers makes transducers through injection molding. And Lithoz America, which we engaged through MITRE’s Bridging Innovation framework, developed a ceramic 3D printing process to manufacture a diverse array of ceramic structures, including dental crowns and veneers.
This work showcases the importance of connecting the right partners to rapidly develop impactful capabilities that could revolutionize undersea operations
Our researchers worked with these companies to create an entirely new technique to 3D print the tiny ceramic structures used in undersea acoustic transducers.
The research team demonstrated a technology that can create novel transducers with improved properties, such as sensitivity, directionality, and bandwidth. These can be applied to unique undersea missions not well-served by conventionally manufactured transducers, including the activities of small maritime robots known as autonomous underwater vehicles (AUVs).
“This innovation will enable pioneering ways to build transducers with capabilities that were previously only hypothetical,” says MITRE’s Chief BlueTech Strategist Nick Rotker.
“It opens up the transducer design space to enable more-capable and more-efficient platforms to gain a better understanding of what’s going on within our oceans.”
Additive Manufacturing: Big Benefits for Small Sensors
It’s one thing to obtain greater insights under the surface. It’s another thing to do it undetected. That requires advanced acoustic transduction properties to project data in a highly focused direction, making it challenging for third parties to receive it.
Our researchers developed a novel geometric technique to achieve this in a single transducer.
“It’s the difference between shining a flashlight versus a laser pointer, only with sound,” explains MITRE’s Justin Tufariello, the project’s principal investigator. “Rather than advertising your presence to everyone in the area, a platform can now more covertly transfer acoustic data. That brings many potential applications, especially within the national security communities.”
To explore that potential, the prototype is undergoing testing by a U.S. Department of Defense sponsor.
In addition to military applications, the increasing use of AUVs to perform data collection for a variety of purposes amplifies the challenges of underwater acoustics—and the need for solutions. The platforms often carry sensors to monitor the environment, measuring things like temperature and mapping the ocean floor with sonar. But AUVs can’t use the same transducers that large vehicles like submarines do, because of the signal processing and electrical power requirements of those arrays.
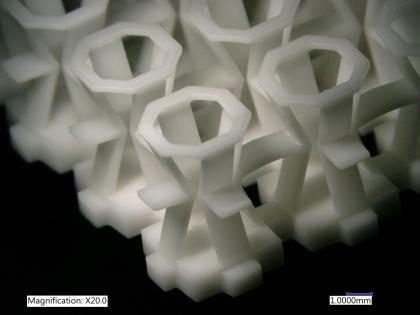
3D-printed ceramic structures, magnified X20.
Our 3D-printed sensors provide these vehicles with customizable transducer options. For small-hulled vehicles, they can offer significant improvements over conventionally manufactured transducers, a process that’s remained static for decades.
The patent-pending technology earned a finalist spot in 2023’s R&D 100. Tufariello and his colleagues also presented findings at the Acoustical Society of America meeting in May.
Ballard Smith, one of MITRE’s independent R&D program leads involved in our transducer research since its beginnings, says the project’s success goes beyond technical accomplishments.
“This work showcases the importance of knowing the problem space and connecting the right partners to rapidly develop impactful capabilities that could revolutionize undersea operations,” Smith says.
Design, Test, Iterate, Repeat
From conception to prototype, the collaborative research team followed a rigorous development and evaluation process, refining the technology along the way. That included proving the additively manufactured transducers work as well as conventionally manufactured ones, under the same challenges.
For example, they had to ensure the structures could hold up under pressure. So, they tested both additively and conventionally manufactured prototypes at the world-renowned Woods Hole Oceanographic Institution, one of our non-profit BlueTech partners. Their hydrostatic chamber can simulate the pressure of the ocean to 10,000 pounds per square inch—just over four miles deep. With roughly 99% of the ocean less than that depth, the testing confirmed the transducer’s durability for use in a wide range of underwater applications.
Additionally, the effort leveraged MITRE’s modeling and simulation expertise to understand the strengths and limitations of different components early in the development process, saving time and effort during prototyping. Our Advanced Manufacturing Lab offered support as well.
The research opens exciting opportunities to expand and advance innovation in the maritime environment.
“We hope this effort will open other cost-effective possibilities for different types of ceramic 3D printing, so we can continue to propel the field of underwater research forward,” Tufariello says.
Join our community of innovators, learners, knowledge-sharers, and risk takers. View our Job Openings.